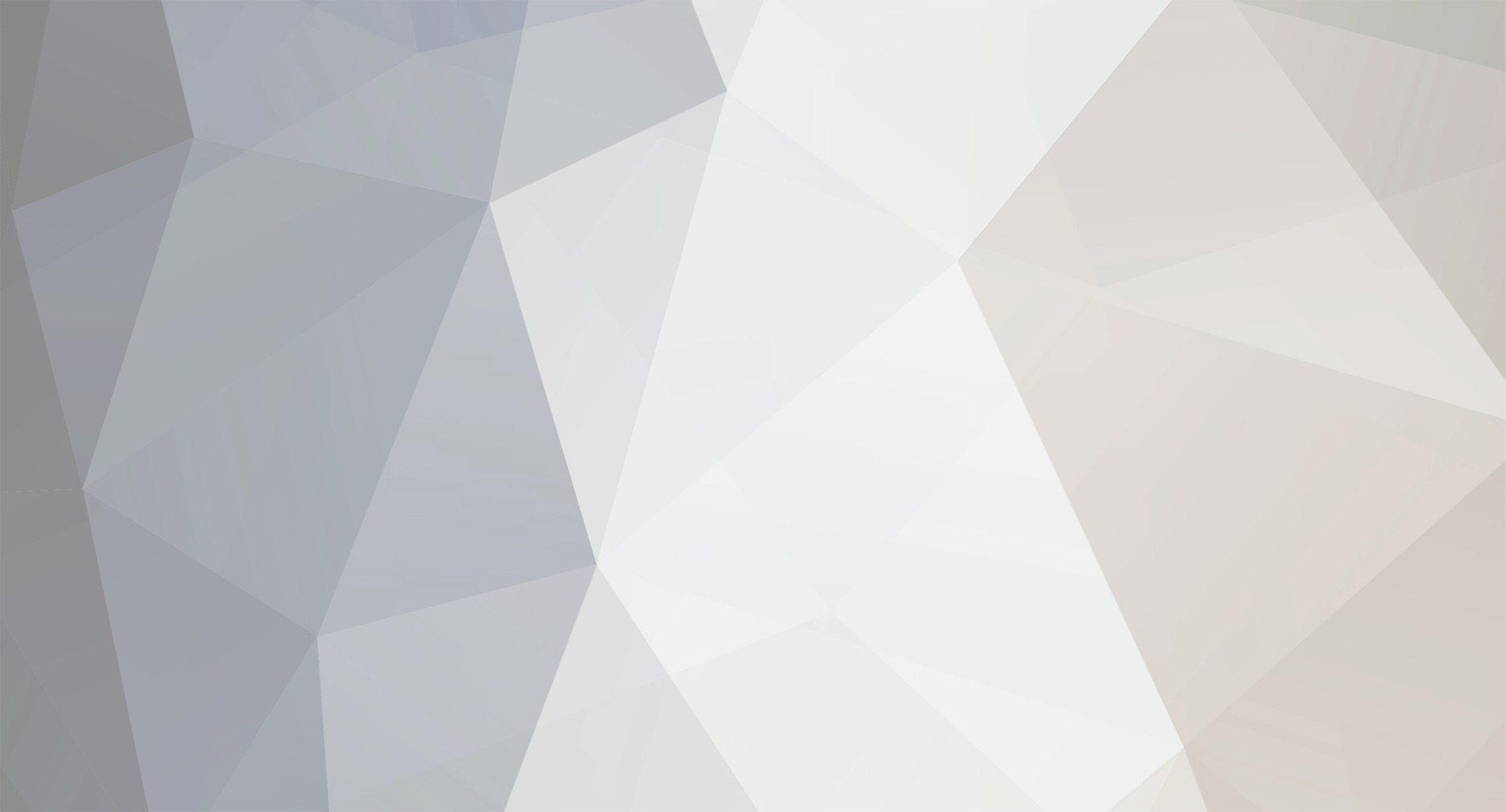
TheSchlonz
Members-
Posts
20 -
Joined
-
Last visited
Recent Profile Visitors
The recent visitors block is disabled and is not being shown to other users.
-
No, it is only one conversion. Bezier, splines or vectors are more or less the same, mathematic funktions. DXF is, in the end , the same as the Trumpf GEO format or the 2D format from Wicam. The only reason they put the dxf in another file format is, that they are also able to add the technological information to the file, like the name of the lasertable, the direction of the laser, the different kinds of piercing and the different kinds of approaches to the laser contour. After finishing the part in the programming software, you have 2 layers in your file, one is the geometry an the other is the technology. But both are only able to hold the informations for straight lines or arc`s with a defined start/end point and the radius, so no vectors, bezier or splines. If armada or bystronic machines are able to process such curves, i am not aware off. But as i know that the Wicam software, that is not able to work with vectors, is also often used with these machines, i assume they are not. So the only needet conversion whould be from a vector, bezier, spline based format to one that breaks these curves down to simple arc`s, in a descent quality. As statet before, Inkscape can save as DXF, but you have no control over the result. In most cases, it will split the curves up, but not in little arc`s, but in little straight lines that follow the curve. Also not satisfying. Profirst is another profesional CAD/CAM software, that does an average job in converting from SVG and even BMPs (with a very high contrast). But depends highly on the quality of the source. You see, there are ways to do the trick, but you have to use, at least one more software, and so, less time for my wife.😉
-
PaoloT reacted to a post in a topic: No DXF EXPORT in Designer 2 ..are you serious!?
-
Not exactly. If you use TruTops Burst, which is the programming system made by trumpf, than you read the dxf files (or draw by yourself) and then save the geometry in the geo file format. We in our company use PN4000 from Wicam instead, which has also its own file format, but the source is allways the same. Meanwhile these CAD/CAM system are also able to import 3D files, althoug our lasers are 2D machines only. The statement, that trumpf can handle BMP, is more marketing. Sure, our system also can read all these file formats, but in the end, the resulting geometry is a complete mess. PDF is an exception, because it can store the complete (correct) information of a dxf or stp file. So your CAM System only needs a filter for PDF import. Vector based file formats are also providing all the information required for a coorct geometry, but you have the problem with the vectors/splines. All others, like bmp, jpg or tiff are pixel based files, where a software can make a black/white image from, if there is a high enough contrast, but i am sure you dont want a part that is lasered with the result from that conversion.
-
Nothing they mentioned is wrong, all other interpretations are up to you. (And, as i said, me) But no mather how long we discuss this matter, nothing will change the fact, that the designer is nit abke to export to dxf. I am with you, in terms, that for me it would also a benifit if (and thats the importent part) the designer would be able to export an "above average" dxf file, or at least comparable to the quality of inkscape. That would save me the need of using one more tool to get what i realy want, and at least time, that i, no matter what i do, have not enough off. BTW: if i would use my time to work with my average tools, instead of writing in this forum, i would be able to spend some time with my loving wife. .
-
I dont know of your finaciel situation, but i think that the price you have to pay for the designer, no matter if there is a export tool to dxf or not, is much lesser than the worth of the tools you get to make some cool designs. As mentiomned, i also would prefer a export filter to DXF, and also was blendet by the loge you postet above, but i still be satified with the tools i get for the price. The only thing a was NOT amoused was, the first time i saw that there is a version 2 for that i have to pay more as for the first version, cause i thought that i have to buy the designer once in my live and will be getting all the future updates. In hindsighte, i think this was a stupid assumption.
-
The laser cutter we are using are machines from trumpf, a german factory. One of those lasers cost about 800.000 k up to 1 million Euro and have 6 kw power. We have 3 of them in use. One CO2 and 2 fiber laser. We laser daily steel, aluminium and stainless steel up to 25 mm thickness, over 1 million KG a year. There are other factorys that produce laser cutter in this class, like bistronic or armada, but they are all limitted to the use, finally in the operating system of the machines, to the contoll system of G-Codes. So they all need, in the end, DXF files, because its industrie standard and fits the most the norm that common CNC machines are using. We also have some 5 axis lathe machines and 3 and 5 axis milling machines. The programming system for those machines is using mostly STP files, that came out of tools like Solid Works, Solid Edge or Inventor. But finaly, the code that comes out of this system is also G-Code, with thousend of lines of code.
-
So, i am back. CNC machines, as a laser cutting machine is, work since almost 1958 in G-Code. This code is only able, to tell the machine that it has to move in a straight line or in an arc. For this the machine gets the information of the ending point from the current position, and in case of an arc, also the radius and the coordianates of the radius. And exactly so is DXF. DXF Files are nothing more than textfiles, that describe the start-end point of the line, and in case of an arc, the radius. With software, like the designer, you can make vectors, also caled splines, to describe a curve, that is constandly changing its radius and this is exactly the point where the problems begin. To translate this to a dxf file, you have to split up the vector in little sectors, define them with a radius and so on. In the ende, the result is a very large number of very smal arcs, that your machine has problemes with to handel, or you get a imprecise and rough contour, with dents on the transition of the arcs. There are very liitle prgramms, that can handle this problem. As mentioned, Inkscape is free and can export to DXF, but the result is often, that you have over 100k on lines in your file, what will couse your programmsystem to collaps. Therefore i use, also as mentioned polyline reducer, that is able to shrink down the file extrem, without loosing the precision.
-
I am also missing the export to dxf feature, but there are free ways to do so, but with a little extra work. Inkscape is a free vector based drawing tool and is able to export to dxf. The bad news about this is, the more vectors you have in the drawing, the more very small lines will be in the dxf file. But you can fix this by using a small, incredible tool, named polyline reducer. Sadly it's not free, it costs 89 Euro, but it's amazing an worth every cent. I use this combination since years in a company which 3 laser cutting machines, to prepare files that I get from Profesional designers that can only provide vector based file formats like svg. AD is a great tool to design and I think, it would be a great benefit (for me) if the dxf export would be implemented. I, for my part, do not understand for what reason there is a dxf import function.
-
bgspa reacted to a post in a topic: DXF or DWG file import in Affinity Designer
-
David.P reacted to a post in a topic: DXF or DWG file import in Affinity Designer
-
I also work with lasercutting machines and need dxf or dwg files for them to work. In my case, i draw with AD and then export to SVG, load that file to "inkscape" (thats for free) and then export to DXF. The DXF files that Inkscape exports are very messed up, because the curves are split up in a lot of small lines. So for that problem i have an amazing tool called "CNC Polyline Reducer", whitch makes radii out of the little lines. It would be easier if i could handle this hole process with AD, but it works fine for me.
- 404 replies
-
using brushes inside shapes
TheSchlonz replied to Emerald15's topic in Tutorials (Staff and Customer Created Tutorials)
Hmm, doesn't seem to work for me. Maybe its because i want to draw with a pixel brush. I did a workaround with - Expand Stroke - select booth - add - divide- delete the outer - an than i have a shape of the inner that i can brush. But its a little bit of work. -
using brushes inside shapes
TheSchlonz replied to Emerald15's topic in Tutorials (Staff and Customer Created Tutorials)
Is there a way to get this to work on a group. For example, i have grouped 4 overlapping Vectors that are not connected. How can i achieve that the lines are work as a border for my brush tool? -
I am using a tablet in AD have bound the Zoom function to one of my 8 tablet buttons. Stopping the Zoom function on releasing the button would be a great improvement for me rather than pressing the Button twice. For the Hand Tool there are 2 Keyboard Shortcuts working. H for toggle the Hand Tool on and off and Space, that keeps the Tool working as long as the button is pressed. (My preferred Binding)